THE COSTER-FROMANTEEL CONTRACT
John C. Taylor
John Fromanteel's
BRASS AND STEEL
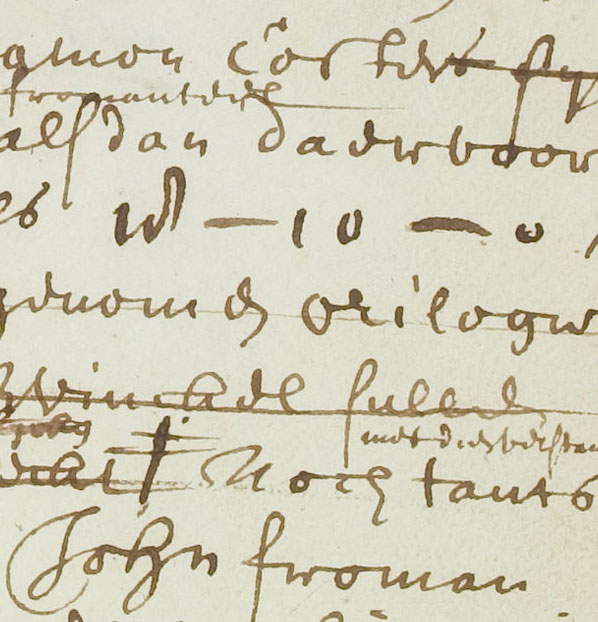
Type
Ctrl+F
to find any text on this page
It has been widely accepted that,
after Huygens adapted a table clock to be controlled by a pendulum and
transferred his patent rights to his design to Salomon Coster, Ahasuerus
Fromanteel in London heard of these new pendulum clock developments and
arranged to send his son, John, who had just finished his
apprenticeship, to The Hague to learn this new construction at
firsthand. A contract was drawn up in The Hague to set the terms of
John’s wages and this technology transfer from Holland to England.
In this article I set out to show that the actual wording within the
contract itself does not support the above synopsis. Rather I submit
that the contract was drawn up under the premise that John travelled to
Holland ready to start work, knowing the layout of the clock trains he
contracted to make. I submit that John brought to Coster’s workshop all
his own brass castings and the necessary steel with him to work for nine
months. The contract was necessary to ensure that John was paid not only
for his labour and his brass and steel but also high enough fees to
cover the design and development costs of the clock in London. It also
ensured that Salomon was forced to purchase all John’s production of
clocks from these kits of parts he brought with him. If John used up his
own brass and steel, only then would Salomon supply him with further raw
materials and John’s fee would be reduced.
There are five extant early domestic pendulum timepieces
signed by Salomon Coster; Dr Reinier Plomp points out their
similarity and agrees with L.H.J. van Lieshout’s suggestion
that all these movements were made under contract by John
Fromanteel for Coster
(1. They all have
similar sized plates, square pillars
(2 and a delicate,
pleasing train of brass wheels driving steel
(3 pinions.
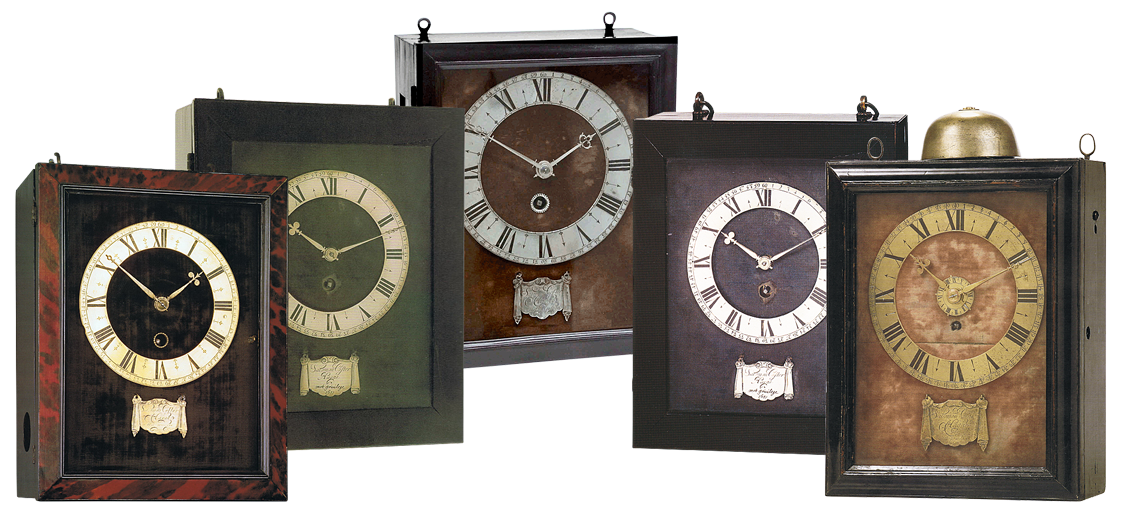
The contract between John Fromanteel
and Salomon Coster has been subjected to much detailed analysis over the
years. One aspect of the contract that appears to have excited little
scrutiny by any reviewer, is the monetary consideration to be paid by
Salomon to John for the clock movements that he produced. In the
translation by Frits van Kersen the signed contract reads:
... for each piece [clock movement]
being of brass and steel, therefore he Coster will pay him a sum of
twenty car. guild.
This clause assumes that John will
most likely supply his own brass and steel and receive twenty guilders.
This conclusion is further strengthened by the exception that now
follows:
And if the aforementioned brass and
steel will be delivered by aforementioned Salomon Coster himself, [ie if
all the brass and steel are supplied by Coster] then he Fromanteel
therefore will enjoy no more as 18-10-0,(4
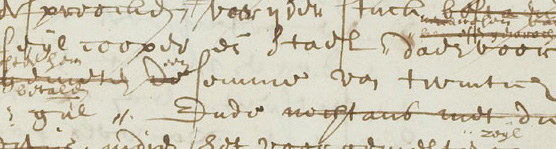
Coster clocks Price list in
guilders, Jan. 1659
|
Weight |
Spring |
Striking |
30 hr. |
8 day |
Price |
● |
|
|
● |
|
48 |
● |
|
|
|
● |
60 |
● |
|
● |
● |
|
80 |
|
● |
|
● |
|
80 |
|
● |
● |
● |
|
120 |
● |
|
● |
|
● |
130 |
|
● |
|
|
● |
130 |
In a letter by Huygens to Boulliau dated 16 January 1659
we find a specification of the various clocks deliverable by
Coster, including prices.
Dr Reinier Plomp gives ‘the price of
a complete Coster timepiece going 30 hours, listed by Huygens as D.fl 80
...’.(5 This is the retail price; Huygens’ letters do not contain
information on Coster’s ex-works price.(6
This is not the place to discuss Business School type market theories
such as ‘Demand for a product increases at least tenfold if the price is
halved’, but this retail price of eighty guilders, set for the world’s
first accurate to a minute domestic pendulum timepiece, has to achieve
two interlinked but different competing objectives:
1. The price has to be low enough to
entice buyers. If the price is set too high there may be no buyers to
come forward to purchase these new but unproven clocks. People in
general do not like to be the first to buy an innovative but untried
product.
2. The price has to be high enough to
restrict sales. If the price is set too low, Huygens would have been
overwhelmed with orders that Salomon would be unable to fulfil. If goods
are not delivered promptly customers quickly become disillusioned and
cancel their orders; they fear the possibility of a swindle: the product
is then condemned by word of mouth making further sales virtually
impossible. An insatiable demand from too low a price would result in a
huge loss of face for Huygens. A further Business School theory is: ‘It
is always possible to reduce price but it is difficult or impossible to
increase it without killing all the product’s pent up demand.’ It would
appear that Huygens did set his retail price high enough to ensure he
was not overwhelmed with orders that Salomon was unable to fulfil; thus
his eighty golden guilders was therefore a high price.
The modern perceived
wisdom of the seventeenth century is that labour was cheap and materials
were expensive. However, John’s labour costing 18½ guilders and the
materials in the movement costing only 1½ guilders, appears to turn
this generalisation on its head to expensive labour(7 and cheap
materials.
After paying John his direct cost for
his materials and labour, Salomon’s ex-works price still had also to
cover the costs of the dial, velvet, silver or silvered chapter ring and
lambrequin, hour and minute hands, wooden case with its door, glass and
lock with the key, two pairs of hinges and hanging eyes and all the
materials and labour. More direct costs were involved in final assembly,
setting up the pendulum, bringing to time and testing. Each clock then
had to be partly disassembled, carefully packed most probably into a
custom-made transit wooden box before the whole was wrapped in
protective padding such as being sown into a hessian sack; then there
are all the costs of delivery. In addition, Salomon’s overheads included
his own wages, rent and taxes on his workshop, repairs and maintenance,
heating, lighting, legal fees, interest and finance costs, postage and a
host of other small business costs.
Huygens then had to unpack and check
the clocks for delivery damage, repack, deliver and set up the clock for
his customer as well as finance the whole transaction. He had his patent
fees, travel costs and advertising correspondence. He had Horologium for
the scientific kudos and, although his correspondence may remain silent,
I find it difficult to believe that he went to the trouble and expense
of patent applications together with the delivery costs if this
broughthim no personal pecuniary advantage.
Thus John’s labour appears a very
high percentage of the final retail price in comparison with Salomon and
Christiaan’s large additional costs and overheads.
In the translation ‘And yet with that
condition: if the aforementioned brass and steel…’ the original Dutch
‘indien’ may be more literally translated into ‘in case’ further
changing the emphasis slightly ‘And yet with that condition: in case the
aforementioned brass and steel...’. The contract uses ‘if ’ or ‘in case’
to imply an unlikely event rather than stating ‘when’ to imply a likely
event that Salomon has to supply (all) the brass and steel to John
whereby John receives only 18½ car.
gld.
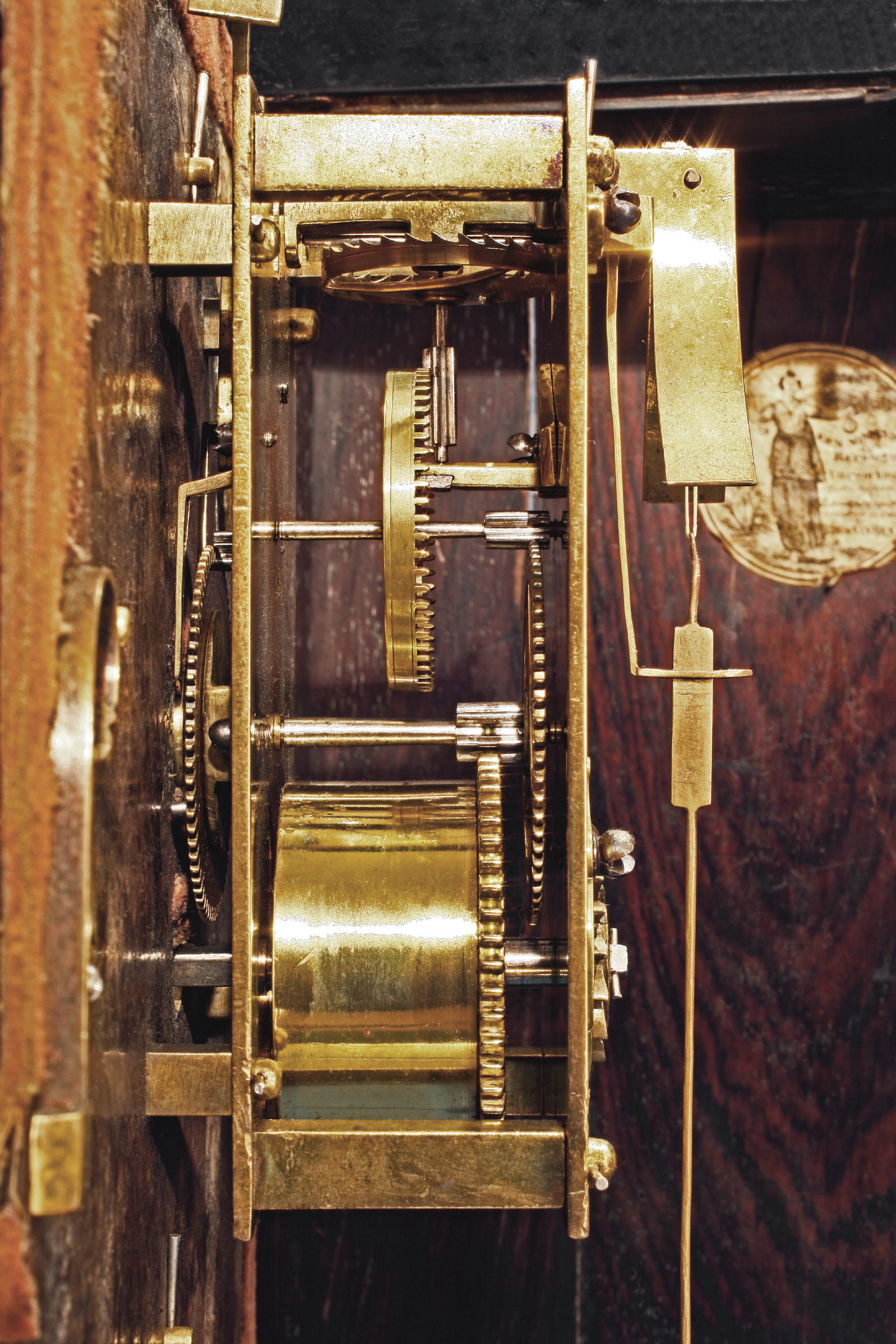
Fig. 1 Side view of a John
Fromanteel movement in a Coster timepiece dated 1658, showing the
movement. Note the square pillars, typical for Fromanteel’s early style.
Thus it is logical to assume John was to start off supplying all his own
brass and steel and Salomon would take over the supply if and only if
John had used up all his own brass and steel.
We can draw four
conclusions from this clause on the fee in the contract:
1.
It assumes that John will most likely supply all his own brass and steel
and receive twenty guilders for a completed movement.
2. This
is an all or nothing requirement, no consideration is postulated in the
agreement if John has to obtain even one small piece of brass or steel
from Salomon. Thus neither of the signatories to the contract considered
this a likelihood.
3.
In the unlikely event that Salomon has to supply John with all the
necessary brass and steel for a complete movement, John will only
receive 18½ guilders.
4.
John’s labour was particularly costly at 23 per cent of the 80 guilders
retail selling price of the finished clock.
The above conclusions
raise further questions that are the crux of this article:
1.
Why should John’s labour appear so expensive?
2. How
did John Fromanteel know what brass and steel were necessary for the
clock movements he was contracting to make?
3. From
where did he obtain his brass and steel that the contract assumes that
he will use? There is no mention in the contract of wood for the clock
cases, velvet dial covering, nor of silvered parts and engraving and it
is generally accepted that ‘each piece’ in the contract refers solely to
the clock movements. Salomon was to supply the rest of the visual
components, dial, etc. and the complete case.
Some of the Coster signed
clocks have brass dial plates and some have steel dial
plates.(8
The five extant movements
supplied by John under the contract are all very similar with matching
sets of brass component listed in Table 1.
All twenty-nine brass
parts were made from twenty-five different types of castings, each
requiring their own patterns.(9
The raw castings had to be hammered to toughen up the soft brass and
then worked and filed up into precision parts for the clock. For
example, the flat spring barrel casting would be hammered round, the
ends brazed together and then turned on a pole lathe to perfect size.
Wheel cutting engines, I understand, were not yet perfected and wheels
and pinions were marked out and sawn and filed to shape. This was the
work that John was undertaking together with forging, turning and filing
the main steel parts. These would most likely have been made from steel
bar or rod and have been as listed in Table 2.
End
of this section, click
here to continue.

NOTES
|
|
1 |
Reinier Plomp, ‘The Prototypes of ‘Hague Clocks and ‘Pendules
Religieuses’ ’, Antiquarian Horology 30/2 (June 2007), 196-208,
esp. pages 198-9 (listing the five known timepieces), 201 and
Conclusion 2 on p. 208. |
2 |
Square pillars are a feature of the earliest extant English
pendulum clocks signed by Ahasuerus Fromanteel, see exhibits 7
and 8 in the catalogue of the 2003 AHS exhibition Horological
Masterworks. |
3 |
I make no differentiation between ‘steel’ as quoted in the
translation of the contract and ‘iron’ as often referred to by
Dr Plomp in his articles, as I feel both words are intended to
describe the ferrous material in common use at the time. I
simply use ‘steel’ throughout for consistency. |
4 |
Frits van Kersen, ‘The Coster-Fromanteel Contract Re-examined’,
Antiquarian Horology 28/5 (March 2005), 561-67. I am grateful
for Frits van Kersen for helping with the nuances of the Dutch
language together with the chronology and help in correcting my
dyslexic orthography. All mistakes remaining are entirely my
own. |
5 |
Plomp, ‘The Prototypes’, p. 201. D.fl = Dutch florin is
interchangeable with a Carolus guilder. |
6 |
H.M. Vehmeyer, Clocks, Their Origin and Development
1320-1880 (2005), p. 227: ‘Coster’s function seems to have been
limited to the contacts with Huygens and the actual production’. |
7 |
Vehmeyer, Clocks, p. 225: ‘the average worker earned at best 40
guilders in a whole year’. |
8 |
Plomp, ‘The Prototypes’, p. 200. |
9 |
At the AHS reception on 26 February 2008 at the Oxford Museum
for the History of Science for the display of the newly restored
Ahasuerus Fromanteel roller cage longcase of c. 1661, the
restorer Matthew Read made the point that all the brass wheels
were cast with the crossings in place. Under close examination
he could still observe the finishing to clean up the casting
surfaces on the crossings. |
10 |
G.F.C. Gordon, Clockmaking Past and Present (1946), Materials p.
5, Motive Power p. 65. See also Vehmeyer, Clocks, p. 225:
‘Generally speaking, the latter type [spring driven] are more
expensive’ [than weight driven]. |
11 |
Percy G. Dawson, C.B. Drover and D.W. Parkes, Early English
Clocks (Antique Collectors’ Club, 1999), p. 7. |
12 |
J.H. Leopold, ‘Some more thoughts on the Coster-Fromanteel
Contract’, Antiquarian Horology 28/5 (March 2005), 568-70 (p.
568). |
13 |
Van Kersen, ‘The Coster-Fromanteel Contract Re-examined’, p.
563. |
14 |
Rebecca Pohancenik, ‘The Intelligencer and the Instrument Maker:
Early Communications in the Development of the Pendulum Clock’,
Antiquarian Horology 31/6 (December 2009), 747-56; esp. pages
747 and 752. |
15 |
Huygens’ Legacy: The Golden Age of the Pendulum Clock at
the Royal Palace Het Loo, 2004, exhibits 5 and 6 in the
catalogue. |
16 |
I am indebted to Michael Hurst for this information. |
17 |
Plomp, ‘The Prototypes’, p. 208. |
18 |
Plomp, ‘The Prototypes’, p. 196. |
19 |
Huygens’ Legacy, exhibit 8 |
20 |
E.L. Edwards and R.D. Dobson, ‘The Fromanteels and the Pendulum
Clock’, Antiquarian Horology 14/3 (September 1983), 250-165 (p.
253). |
|
|
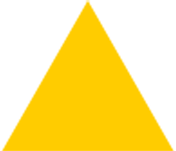
|
Table of contents:
This
article was first published in the Sept. 2010 issue of Antiquarian
Horology.
Technically the most difficult
steel part is the clock main spring. Each clock design
requires a unique motive driving energy store, matched to
the duration, the particular train and the chosen pendulum.
The spring in the Coster timepieces is particularly
difficult as no fusee is used to even out the decay in the
spring action as it unwound.
G.F.C. Gordon writes at length
on the problems that the early metal workers had in making
thin steel springs and how only the most costly movements
were spring driven. He writes ‘…for one satisfactory bracket
clock spring which was made and used, ten or even fifty were
tried and rejected.’(10 This large, easily seen, spring
driven domestic timepiece, accurate to show meaningful
minutes for the first time ever, was the pinnacle of
scientific achievement and technological manufacturing: in
modern terms, high technology, coveted consumer designer
product; the expensive ‘must have boys toy’ from the middle
of the seventeenth century. Huygens reports in his diary
that he had the pleasure of adapting his first model
pendulum clock on Christmas Day 1656 and by June 1657 a
patent had been granted to Salomon Coster.(11
TABLE
1 |
Casting patterns |
Brass parts |
|
Front plate and back plate |
1 |
1 |
Square movement pillars |
1 |
4 |
Great wheel, spring barrel and barrel cap |
3 |
3 |
Click wheel and click spring |
2 |
2 |
First wheel |
1 |
1 |
Contrate wheel |
1 |
1 |
Escape wheel |
1 |
1 |
Cannon wheel |
1 |
1 |
Minute wheel |
1 |
1 |
Hour wheel and integral pipe |
2 |
2 |
Crutch and crutch block |
2 |
2 |
Pendulum bob and rating nut |
2 |
2 |
Top pottence and bottom potence |
2 |
2 |
Backcock, left and right cheeks |
3 |
3 |
Motion work bridge |
1 |
1 |
Clock winding key |
1 |
1 |
|
Totals |
25 |
29 |
TABLE 2 |
Steel parts |
|
First arbor and pinion |
1 |
Contrate arbor and pinion |
1 |
Escape wheel arbor and pinion |
1 |
Minute wheel pinion |
1 |
Verge arbor and pallets |
1 |
Hook for main spring in brass barrel |
1 |
Winding click |
1 |
Crown wheel lower bearing |
1 |
Tapered
pendulum rod |
1 |
Miscellaneous screws |
8 |
Miscellaneous taper pins |
4 |
Clock spring - the most expensive component in the clock |
1 |
|
Totals |
23 |
Therefore one
might probably assume that casting patterns and raw castings
from a Dutch brass foundry must have been available in Coster’s workshop when John Fromanteel arrived in
The Hague in late summer 1657.
For any subcontractor, it
is financially disadvantageous to supply your own materials.
Apart from your own personal cash tied up in the stock, you
personally stand the loss if parts are lost or damaged or
the dimensions are changed and the components are scrapped.
Any faults or mistakes needing replacement are your own
materials and your personal costs. Thus it is normal
practice and to the advantage of subcontract craftsmen to
solely sell their labour leaving their employer to supply
all the materials on which they perform their work. If
John supplied his own brass and steel, any faulty finishing
work requiring a new raw piece was his own personal
financial loss: it was not in John’s interest to supply his
own materials, particularly if there was any
development still taking place that might make any parts
obsolete. It was to John’s benefit to have Salomon supply
all the brass and steel for him to work up and finish to a
going clock movement. Yet the contract specifically implies
that the most likely scenario is that John, a 19 year old
newly arrived in a foreign land, will take the
responsibility to supply all his own brass and steel! How
and why would he do this? Even with John’s likely command
of the language,(12 if, as suggested,(13 he had worked for a
week or two in Salomon’s workshop, using Salomon’s brass and
steel:
1. It seems inconceivable that John decided that
Salomon’s brass and steel were of inadequate quality, or of
such a high price from the Dutch suppliers that he could
make a profit from supplying his own parts.
2. It appears
unlikely that he could visit Salomon’s local Dutch suppliers
and negotiate a better price than Salomon to make it worth
his while financially to take on the responsibility of
supplying all his own brass and steel.
3. If the castings
were not yet available, it would be unlikely for John as a
young itinerant craftsman to have the cash with him to pay
for the patterns to be produced and finance the necessary
batches of brass castings and necessary steel, particularly
as he only was paid for the materials he used after he had
completed each movement.
4. Equally implausible is the
thought that he had to draw up each and every part and
either send the drawings or took the drawings or a set of
parts back to London to enable a quotation to be prepared
and then sets of parts produced and shipped over prior to
the contract being signed.
5. Nevertheless, he went with
Salomon before a Notary and signed a contract thereby taking
the full responsibility to normally supply all his own brass
and steel.
Rebecca Pohancenik has recently established that Ahasuerus
Fromanteel had indeed manufactured and sold pendulum clocks
prior to John Fromanteel’s sojourn with Salomon Coster. She
also links Christiaan Huygens with Ahasuerus Fromanteel,
giving further insight into the origin of possible technical
collaboration.(14
The
little table clocks by Coster exhibited at Het Loo(15
have beautifully shaped pillars. Square pillars were not a
natural progression for Coster. With no power lathes
available to turn up round and complex shaped pillars, such
attractive shapes took much care and effort to produce on a
bow lathe. All the extant very early pendulum clocks signed
by Ahasuerus Fromanteel have square pillars. These appear to
be unique to Ahasuerus’ signed early pendulum clocks. Square
brass pillars can be produced from a raw casting, not just
by filing but by hammering the brass to a tough regular
shape,(16 leaving just the
two ends to be turned round on a lathe. Moreover, Ahasuerus
was an experienced blacksmith and used to hammering metal
into shape. Coster was under pressure to produce sufficient
clocks to meet Huygens’ demand and accepted the Fromanteel
quicker if less visually attractive option.
It is not necessary for me to postulate
that the springs, brass castings, etc were actually made in
the Fromanteel workshop; they may have been made by
specialists nearby in London; I solely suggest that John
must have brought these components with him to The Hague if
he was to sign a contract to supply them.
I conclude that
John Fromanteel arrived at Salomon Coster’s workshop and
signed the contract knowing what brass and steel was
required and brought with him several complete sets of brass
castings, together with the necessary steel rod and bar, as
well as the necessary clock springs. Only if all these
conditions were met would the contract have been drawn up as
it was.
It was John who needed a contract and had it
altered to ensure he had:
1. A fixed price for the work
and materials he supplied.
2. A guaranteed market for the
movements he produced.
3. A high price to cover any
development work that had already taken place in London and
perfections still to take place in The Hague.
Almost the
last clause in the contract gives John this necessary
assurance:
... provided
the works by which he Fromanteel on the conditions aforementioned will
have been made, he Coster for the stipulated price will be allowed and
obliged to keep.
In other words if John makes the
movements, he is going to sell them to Salomon and Salomon
is required to pay 20 guilders for them. Plomp in his
conclusion no. 2 says:
The movements of the five
Coster timepieces are so similar that it is justified to
conclude that they represent the movements referred to in
the contract between Salomon Coster and John Fromanteel.(17
To this I would add: ‘and made from a kit of brass
and steel parts and the main springs brought with him from
London’.
We may now conclude that there were at the very least
letters, drawings and specifications of the movements passed
between Coster and the Fromanteels before John’s visit in
September 1657. Most likely one or more sample movements
were produced in London before the approval for the
production of the unique brass castings and mainsprings for
John to take with him to The Hague. This also opens for
further discussion the clauses in the contract and a literal
interpretation of the following two phrases:
1. ‘John Fromanteel obliges and
commits himself to execute and perfect his watchwork …’
as an indication that the Coster/Fromanteel design was still
not finalised and some perfection of the mechanism was still
to be undertaken by John. The earliest signed Coster
pendulum clock dated 1657 was found in 1922 by Drummond
Robertson in the Rijksmuseum (as he reports: subsequently
lost) together with the present earliest extant clock also
dated 1657.(18 Whilst the trains were very similar the first
clock solely had an hour hand whereas the later clock also
has a minute hand.(19 Was this the perfection to be carried
out by John?
2.‘…like
he Fromanteel already has made some’ was as a further
substantiation that John had already been producing
prototype Coster pendulum clocks in London. This phrase in
the contract was considered by either Salomon or John or
both as an important additional clause added into the
contract as it is inserted, crossed out and inserted again
in a different place to strengthen the point.
E.L.
Edwards and R.D. Dobson note that the backplate of the
earlier Rijksmuseum clock was signed ‘Samuel Coster Haghe
met privilege’ and point out that signing on the backplate
is an English, not a Dutch tradition. As Salomon corrects a
similar mistake over his name in a contemporary document,
they surmise that this clock must have been made by John
without Salomon’s input,(20 to which I would add: ‘in London
prior to his visit to The Hague’.
I conclude that the Fromanteel family expertise
facilitated in preparing the Fromanteel/Coster design in
London so that the necessary kits of brass castings and
steel together with the mainsprings could be produced for
John to take to The Hague with him, ready to start work. But
it was necessity for John to have a contract to ensure he
was paid a suitable high fee as this was also to cover the
Fromanteel development work in London and not just his own
labour costs. This can all be deduced from the contract.
About the author
Dr John C. Taylor is an inventor with about two hundred
British patents in his name. The company he founded in 1981 won
four Queen’s Awards and last year celebrated selling one billion
kettle controls. His interest in horology started through
navigation – trying to fly a small aircraft from Manchester to
Tokyo. His latest invention is the Corpus Chronophage.
(john@fromanteel.com)
ACKNOWLEDGEMENTS
The Horological Foundation is endebted to the Antiquarian Horological
Society for making their PDF version of the original printed article
available.
Photo 1: Courtesy of Dr. John C. Taylor, Isle of Man
May
2019, Copyright: John C. Taylor
LINKS
Chr.
Huygens' Œuvres Complètes.
(pdf)
Chr.
Huygens Horologium 1658.
(pdf)
The Coster Fromanteel Contract. The Van der
Horst transcription working sheet. (also
PDF)
(This article is subject to ongoing
revisions.)
|